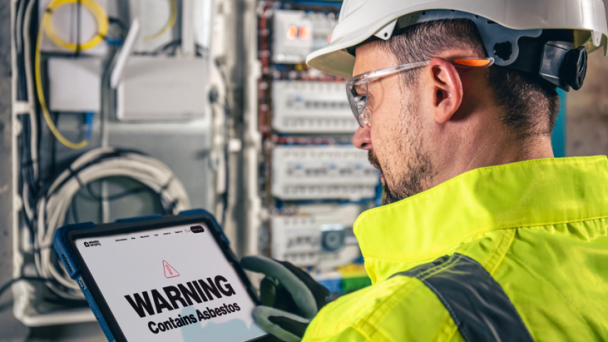
Asbestos is regularly delaying fibre projects by one-to-two weeks whilst remaining the single biggest killer of tradesmen in the UK, according to Tom Yates, Director at TYSR. Here, he calls on altnets to bring testing in-house cut asbestos-related delays down to 24-48 hours and bring savings of over 60% per site.
Q1) Why do fibre providers need to take more notice of asbestos testing
Asbestos is still present in a huge number of buildings across the UK, especially those built before 2000, which covers the vast majority of MDUs and older residential or commercial premises. Here asbestos is still present in risers, service cupboards, or common access areas, especially in the form of artex/textured coatings on walls and ceilings.
For fibre providers and contractors working on tight deadlines, asbestos can cause significant disruption as access for third-party surveyors is a major challenge, residents must be notified, visits need to be coordinated, and this adds complexity and time.
We regularly hear about projects being delayed by one or two weeks simply because an asbestos survey hasn’t been done or isn’t available. In many cases, contractors are ready to proceed, but can’t disturb certain materials until samples have been collected, sent off, and analysed, a process typically handled by third parties with their own scheduling and access challenges. That delay adds up quickly, especially across a high-volume fibre rollout.
Q2) How can this be improved by bringing testing in-house?
Engineers conducting initial surveys are already on-site and can carry out sampling at the same time, without added disruption. New builds are not of concern in terms of asbestos, but this approach is particularly valuable in urban retrofit projects, where older infrastructure meets new fibre installations.
By bringing sampling in-house, providers can cut asbestos-related delays from 1–2 weeks down to 24–48 hours. Sample results are typically turned around the next working day, and the engineer can move forward as soon as they’re cleared.
In terms of cost, the savings are significant. Our solution avoids the call-out fees, admin charges, and overheads that come with external surveyors. On a per-site basis, clients often see savings of over 60%, and when rolled out across an entire build program, this can translate to tens of thousands if not hundreds of thousands of pounds saved—not to mention the value of staying on schedule.
Q3) Have you worked with other fibre providers?
Yes, we’re currently working with several infrastructure contractors and fibre providers operating in both urban and rural builds. The feedback has been consistently positive. One major infrastructure client reported that using our service helped them avoid delays on over 70% of the jobs where asbestos issues would otherwise have slowed them down.
We’re also in active discussions with several altnets who see this as a key enabler for faster, safer rollout, particularly in retrofit scenarios.
Q4) What is the process for bringing this in-house?
We provide everything a contractor needs to collect samples safely and compliantly, including guidance, lab access, and ongoing support. Engineers are trained in how to take samples properly, using a straightforward & compliant process.
Once a sample is taken, it’s sent to a UKAS-accredited lab in our network using our tracked return service. Results are typically returned within 24 hours of receipt, and clients are notified by their preferred method (email/phone) and via our online portal.
Importantly, this is not a substitute for full surveys where required—it’s a targeted solution for contractors needing quick answers about specific materials before work can proceed.
Q5) Many altnets avoided contractors during build phase due to reputational damage – how are you ensuring efficiency, safety, and compliance?
We understand the importance of protecting both reputation and compliance. Our service is fully aligned with HSE guidance and samples are processed by UKAS-accredited laboratories. Every step is documented, traceable, and built with compliance in mind.
We also focus on clear, practical training, ensuring contractors are confident and competent in the process. Our kits are designed for safe, simple use—and we’re always on hand for support. For fibre providers using subcontractors, it’s a way to maintain control and oversight, while reducing the risks of relying entirely on external surveying teams.
~If you’re interested in exploring how in-house asbestos sampling could benefit your organisation visit our website at tysr.co.uk. Alternatively email fibre@tysr.co.uk to arrange a call or discuss your specific requirements further~